The evolution of 3D printing has transformed industries and opened up new possibilities for innovation, manufacturing, and design. What began as a niche technology has now become a key player in sectors like healthcare, automotive, aerospace, and fashion. 3D printing, or additive manufacturing, allows for the creation of three-dimensional objects by adding material layer by layer, based on a digital model. In this post, we will explore how 3D printing has evolved over the years and its current and future impact.
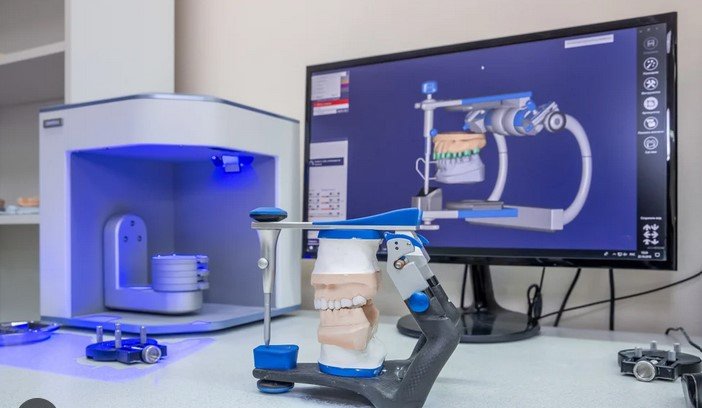
1. Early Days of 3D Printing
The origins of 3D printing trace back to the 1980s. In 1983, Chuck Hull invented stereolithography (SLA), the first 3D printing process. Hull’s technology used ultraviolet lasers to solidify liquid resin layer by layer, forming three-dimensional objects. This innovation led to the creation of the first 3D printer, known as the SLA-1, which was designed primarily for rapid prototyping in the manufacturing industry.
At this stage, 3D printing was expensive and not widely accessible. It was mainly used by large corporations to create prototypes and models quickly and efficiently, reducing the time and cost of traditional manufacturing methods. The process was complex, and the materials used were limited. Despite its potential, 3D printing had yet to gain widespread attention.
2. Advancements in Materials and Technologies
In the 1990s and early 2000s, 3D printing technology saw major advancements, particularly in materials and process capabilities. New types of 3D printing methods were introduced, such as fused deposition modeling (FDM) and selective laser sintering (SLS), which expanded the range of materials used in 3D printing.
FDM, developed by Scott Crump in the late 1980s, became one of the most widely used 3D printing methods. It involves melting plastic filament and extruding it layer by layer to create objects. FDM opened the door for more accessible and affordable 3D printers, leading to their adoption by small businesses, educational institutions, and even hobbyists.
Meanwhile, advancements in material science allowed for the use of more durable materials, including metals, ceramics, and even bio-compatible materials for healthcare applications. These developments enabled industries to explore new possibilities, such as 3D-printed prosthetics, metal parts for aerospace, and customized medical implants.
3. The Rise of Consumer 3D Printing
By the 2010s, 3D printing experienced a shift toward consumer-level applications. The introduction of affordable 3D printers, such as the MakerBot and RepRap, brought 3D printing into homes and small businesses. These consumer-friendly printers were more accessible, offering individuals the ability to create everything from toys and jewelry to tools and home decor.
At the same time, open-source 3D printing communities began to thrive. The RepRap project, which aimed to create a self-replicating 3D printer, helped democratize the technology. Users could download designs, modify them, and share their creations with others. This led to an explosion of creativity and innovation, as individuals and small startups explored new ways to use 3D printing.
As consumer-grade printers became more affordable, the scope of applications grew. 3D printing was no longer limited to prototyping; it was now used for creating end-use products, custom items, and even art. The ability to print in various materials, from plastics to food and even human tissue, was a game-changer, pushing the boundaries of what could be created.
4. 3D Printing in Industry and Healthcare
As 3D printing technology advanced, its use in industries like healthcare and manufacturing became more widespread. In healthcare, 3D printing revolutionized prosthetics and orthotics. Custom prosthetic limbs could be created quickly and tailored to the patient’s specific needs. Medical researchers also began to explore 3D printing for creating custom implants, surgical tools, and even human tissues.
In manufacturing, 3D printing enabled companies to reduce production costs and time by printing parts on-demand. It also allowed for the creation of complex geometries that were previously impossible to manufacture using traditional methods. Industries such as aerospace, automotive, and electronics now use 3D printing to create lightweight, durable, and customized parts, significantly improving production efficiency and product design.
5. The Future of 3D Printing
The future of 3D printing holds tremendous potential. Researchers are continually pushing the boundaries of what can be achieved, with ongoing developments in speed, materials, and precision. One exciting area of development is in bioprinting, where scientists are working on printing human tissues and organs. While we are still a long way from printing fully functional organs, progress in this area could revolutionize healthcare and organ transplantation.
Moreover, advancements in 3D printing could help solve sustainability challenges. With the ability to print products on-demand, waste could be reduced in manufacturing. Additionally, the use of recycled materials in 3D printing is growing, allowing for more eco-friendly production methods.
As 3D printing becomes more advanced, it will likely continue to impact a wide range of industries. From manufacturing to healthcare, architecture, and even food production, 3D printing will continue to transform the way we design, create, and produce goods.
Conclusion
The evolution of 3D printing has been nothing short of remarkable. From its beginnings as a rapid prototyping tool to its current status as a game-changing technology in industries like healthcare, manufacturing, and consumer goods, 3D printing has reshaped the way we think about design and production. As the technology continues to evolve, its applications will only expand, offering new opportunities for innovation and creativity across many fields.